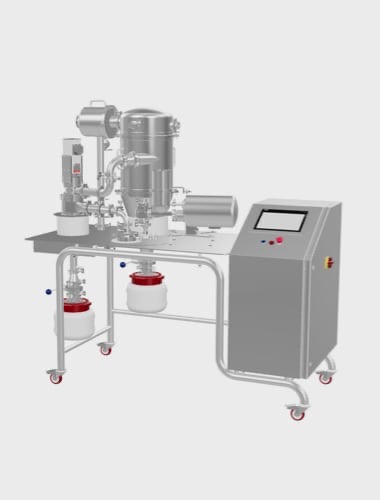
Particle Size Control Technology
The poor solubility of indissolvable drugs affected the bioavailability of the drugs seriously, so the control to the particle size of indissolvable drugs is one of the methods to improve the solubility thereof. We can provide wet mill, jet mill, crushing machine and the like to control the particle size of indissolvable drugs, so as to increase the specific surface area of particles significantly and improve the solubility of indissolvable drugs.
Specifically, the work principle of jet mill is to drive materials to rotate at a high speed within the chamber through high pressure airflow, and crush the materials through the collision and friction among the particles and between the particles and the chamber. The material can be crushed to 0.5-10 microns. In addition, wet mill is a milling technology of crushing drugs to nanometer level through high strength mechanical energy, in which the particles milled are dispersed in a specific substrate and remain stable for a long time. Both techniques significantly increase the specific surface area of the API to increase the dissolution rate.
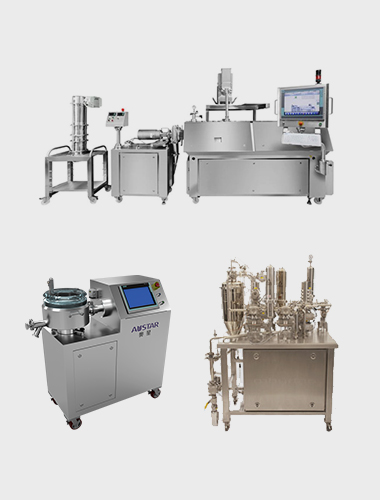
Granulation Technology
AUSTAR can provide a variety of solutions to meet the developmental requirements of users on product granulating process, such as high-shear wet granulation, fluid-bed granulation, twin-screw extrusion granulation, hot-melt extrusion granulation, melting granulation, dry granulation and spray drying. The granule size can be controlled by adjusting granulation process, so as to improve the fluidity, roundness, appearance, abrasion resistance, compressibility and bioavailability of the particles.
Hot-melt extrusion granulation technology is mainly used to improve the dissolution of indissolvable drugs, and to prepare controlled release preparations. Spray drying granulation technology is to use the spray method to make the material dispersed in the hot air in the state of mist. Upon the full contact of the material with the hot air, the heat and mass transfer is completed in an instant. The purpose is to make the solvent quickly evaporates into gas to achieve drying, so as to obtain good fluidity and solubility, and effectively improve the bioavailability of drugs.
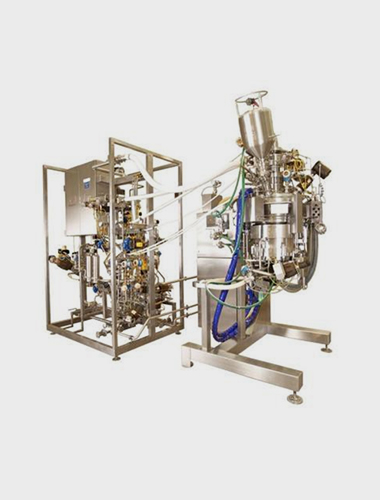
Microsphere Technology
As a modern new drug carrier, microsphere preparation, featured the dispersive and protective functions of traditional drug carriers as well as the effect of sustained release, has a broad prospect of development and application.
AUSTAR can provide micro-jet encapsulation technology. The technology can be used to produce micro-droplets with uniform size by ejecting aqueous-phase liquid and oil-phase liquid with API and accessories through a micron-sized pipe, and form uniform microglobular particles by precipitating and solidifying. The micro-jet encapsulation technology can improve the encapsulation rate of product to API greatly, improve the stability and continuity of product release, and optimize the stability of process amplification based on the concept of micro-channel manufacturing.
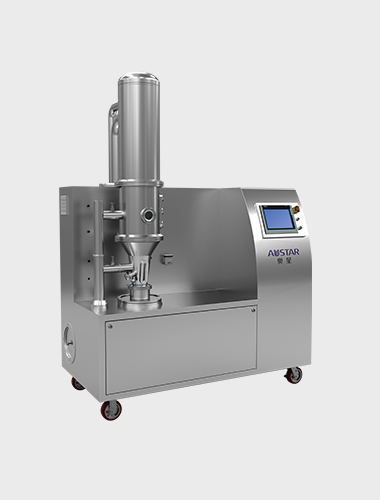
Pellet Coating Technology
The pellet coating system of fluidized bed is to realize the suspension flow of pellet within the coating area through the air flow rising rapidly, in which the pellet will pass through the coating area every few seconds for continuous coating and drying. All pellets have a similar probability of passing through the coating area, so the coating film formed is uniform and dense.
The thickness of pellet coating is the main critical quality attribute that affects the dissolution rate. Moreover, we introduce process analysis technology (PAT) into the production process control system to monitor and control the critical process parameters dynamically to ensure the consistency of product quality, so as to ensure the consistency of product quality. The application of PAT in pellet coating process can analyze the difference between initial and real-time particle size distribution, estimate the thickness of the real-time coating film, and further track and analyze the particle size distribution during the coating. To some extent, a prediction model for the dissolution of the coating film can be established, which can shorten the R&D cycle of the controlled release pellet coating drugs.
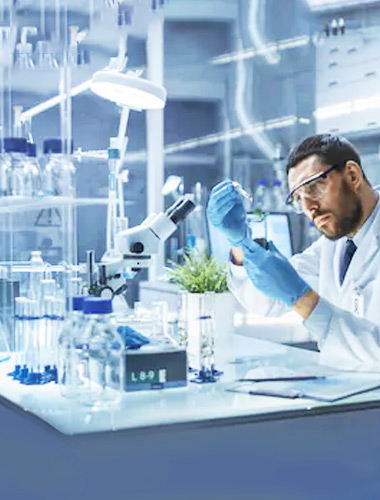
Powder & Solid Technology Research Center
AUSTAR Powder & Solid Technology Research Center focuses on exploring the product technology from laboratory to mass production for the clients. Equipped with professionals who are engaged in drug research and development for many years, preparation machinery of international famous brands, production equipment that complies with GMP standards for drug production and advanced testing instrument, the research center can carry out a series of studies and researches on powder properties, granulating technology, tableting technology, coating technology, soft capsule technology and hot melt extrusion technology etc. and choose the appropriate processing equipment for clients according to the research result of product technology to finally realize formulation production successfully. The application of advanced PAT equipment in pharmaceutical preparation research enables the clients to have a better understanding of the product technology and guarantees product quality as well as shortening client's R&D cycle.
Another important function of the research center is to provide technology amplification service for clients, which can help clients to complete products transfer from pilot study to intermediate study and establish corresponding document system to meet declaration and inspection requirements.